Реферат: Керамічна цегла: добування і обробка сировини, виробництво
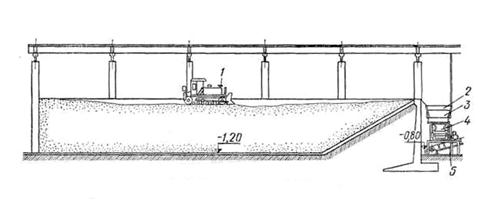
Мал. 15. Глиносховище з бульдозером: 1 - бульдозер, 2 -
бункер, 3 - глиноспушувач, 4 -
ящик подавач, 5 – конвеєр
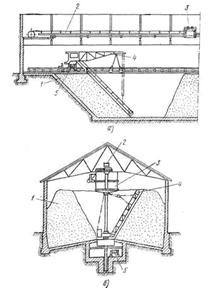
Мал. 16. Стаціонарні глиносховища: а — з пересувними мостами
екскаватором, би — з верхнім черпанням глини; 1 — глина, 2— конвейєр для подач
сировини, 3—- глинооброблююса машина, 4 — екскаватор, 5 — конвеєр для відбору
глини
Сушка глини
Для сушки глини до стану, при якому вона легко дробиться
розмелюється, застосовують прямоточні сушильні барабани, Сушильний барабан (мал. 17)
Циліндром 3, що обертається на чотирьох роликах двох опорних пристроїв 2, на
які циліндр спирається насадженими на нього бандажами. Барабани встановлюють з
нахилом у бік вивантаження. Для попередження осьового зсуву один з опорних
пристроїв має два наполегливі ролики. Бандажі упираються на дві пари опорних
роликів і одну пару наполегливих роликів 5. Між опорами на корпусі барабана
кріплять венцову шестерню,
завдяки якій барабан приводиться в обертання. Обертання на венцову шестерню
передається від приводу 4.
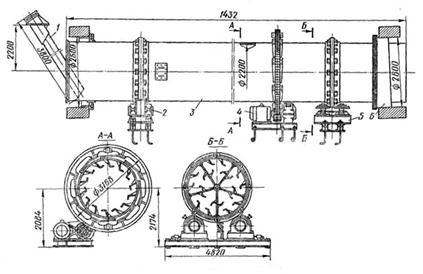
Мал. 17. Сушильний барабан СМ-147А: 1 - живильник, 2 -
опорний пристрій, 3 - циліндр барабана, 4 - привід, 5 - наполегливий пристрій,
6 - ущільнювач
Матеріал, що підлягає сушці, поступає в барабан,
що обертається, через трубчастий живильник 1. Гвинтові направляючі лопат
захоплюють масу і подають її до лопатей насадки. Завдяки нахилу барабана матеріал
переміщається у бік вивантаження. Висушений матеріал висипаеться з барабана
через тічку.
Барабан працює з постійною температурою вхідних
газів — 800° С. При зміні вогкості матеріалу або прискоренні його подачі в
барабан режим сушки регулюють збільшенням або зменшенням кількості газів, що
поступають. Для уникнення конденсації вологи в розвантажувальній камер
температура газів, що відходять, не повинна падати нижче 90° С. Гази
відсисаються з барабана через мультициклон. Щоб гази і пил не вибивалися з барабана,
встановлено кільце ущільнювача.
Технічні характеристики сушильних барабанів
приведені в табл.12.
Таблиця 12
Технічн
характеристики сушильних барабанів
|
Показники
|
СМ-1013
|
СМ-45Б
|
CM-107G
|
СМ-147А
|
7203
|
Продуктивність,
т/ч
|
3,5 |
2,7 |
21 |
15 |
30 |
Температура
сушки °З:
|
|
|
|
|
|
початкова
|
800 |
800 |
700 |
800 |
800 |
кінцева
|
100 |
100 |
100 |
100 |
100 |
Вид
палива
|
Газ, вугілля, мазут |
Максимальний
розмір частинок висушуваного матеріалу, мм .
|
35 |
30 |
60 |
60 |
60 |
Діаметр
барабана, мм
|
1600 |
1600 |
2200 |
2200 |
2800 |
Довжина
барабана, мм
|
8000 |
8000 |
14000 |
14000 |
14000 |
Кутова
швидкість, об/мин
|
6,1; 4,1; |
1,4 |
5,6 |
5,6 |
4-6 |
Кут
нахилу, град
|
3 |
3 |
3 |
2°51 |
3 |
Потужність
електродвигуна, квт
|
10; 9; 7 |
7 |
40 |
28 |
28 |
Габаритн
розміри, мм:
|
|
|
|
|
|
довжина
|
9850 |
10000 |
17 500 |
14 032 |
14 032 |
ширина
|
2800 |
3000 |
3 700 |
3 910 |
4434 |
висота
|
3550 |
3500 |
4 500 |
3 758 |
4 340 |
Маса,
т
|
13,9 |
15,0 |
40,2 |
36,12 |
70,0 |
Сушильні барабани працюють на твердому, газоподібному і Рідкому
паливі. Топки сушильних барабанів виконують виносними.
Приготування шамота
Паралельно з основними процесами виробництва виробів для
облицьовування фасадів на заводі виготовляють шамот. Глину з складу подають
в каменевидільні вальці і потім в змішувач, де вона зволожується і (перемішується
до 15— 16% вогкості, а потім поступає на брикетування.
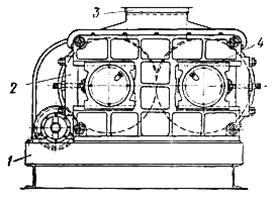
Мал. 18. Пресс-вальці: 1 — станина, 2, 4— формуючі валяння з
сферичними поглибленнями, 3 — завантажувальна воронка
На деяких заводах брикети формують на стрічкових
пресах з пластичної глиняної маси з мінімальною вогкістю, при якій
забезпечується їх формуємість. Такі брикети
виготовляють (у формі прямокутного паралелепіпеда масою 7—12 кг.
Останніми роками для брикетування глини
використовують пресс-вальці (мал. 18). Вони складаються з двох однакових що
обертаються назустріч один одному валів 2 я 4. На зовнішній стороні валів
сферичні поглиблення діаметром 85—ПО мм Ці валяння встановлені таким чином, що
при їх обертанні отвору сполучаються і падаюча в них глина перетворюється на
брикет у формі сплюснутої кулі. Міцність спресованого брикета — 5—7 кГ/см2,
маса — 0,7—1 кг.
Технічна характеристика пресс-вальців
·
Продуктивність, т/ч........................ 26
·
Розмір брикетів, мм.............................. 64X80
·
Ширина валів, мм . ...................... 440
·
Діаметр валів, мм................................ . 850
·
Кількість осередків у валянні, шт. ......... 120
·
Кутова швидкість валів, об/мин .............. 6,6
·
Потужність електродвигуна, квт ... 20
·
Габаритні розміри, мм:
·
довжина ....................... 3545
·
ширина ....................... 2533
·
висота ...................... 1610
·
Маса, т ....................... 7,9
Брикети, що відпресували, діаметром 100—120 мм потрапляють в
очисний барабан (біляче колесо) діаметром 900 мм, що обертається із швидкістю
60 об/мин. Тут щільні брикети очищаються від заусенців, а слабі розбиваються
повертаються на повторне брикетування.
Щільні обчищені брикети поступають в шахтну або обертається піч
для випалення.
Шахтні печі для шамота
Шахтні печі для шамота конструкції інституту Гипростройматеріали (мал.
19) мають елліпсовидний перетин. Вони
викладені з вогнетривкої цеглини, а для додання печі міцності навкруги не
робиться металічний каркас. Щоб попередити підсос зовнішнього повітря через
кладку печі, її укладають в металевий кожух.
Шахтні печі працюють на генераторному або природному газі. Газ
підводиться в зону горіння
через бічні вікна, розташовані по периметру печі. У верхній частині печ
встановлені додаткові пальники, які забезпечують той, що підсушив і виключають
злипання брикетів.
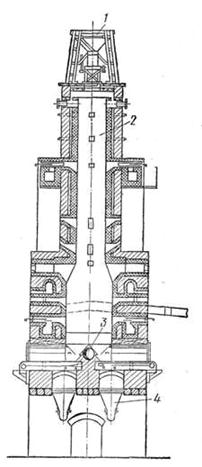
Мал. 19. Шахтна піч: 1 — завантажувальний пристрій, 2 — шахта. 5 патрубок
для відсмоктування димових газів, 4 — механізм вивантаження
Завантажують брикети в шахтну піч
завантажувальним пристроєм 1, яке обладнане шлюзовим затвором. Затвор запобіга
підсосу повітря в піч. При підйомі верхнього затвора брикети з верхнього
бункера опускаються в нижній тічку і звідси в шахту 2 печі. Відсмоктування
димових газів здійснюють через патрубок 3.
Вивантажують обпалений шамот автоматичним
вивантажником 4 системи Антонова. Вивантажник є установкою, що складається з
трьох пар ступенеобразних кареток, що приводяться
в поворотно-поступальний рух за допомогою кривошипних механізмів і системи
передачі від електродвигуна. У міру вивантаження обпаленого шамота завантажен
брикети поступово опускаються вниз, проходячи послідовно зони підсушила,
підігріву, випалення і охолоджування. Продуктивність шахтних печей 60—70
т/сутки.
Печі для випалення шамота, що обертаються,
працюють таким чином. Глина з складу подається в глинорізку (стругач) і звідси по
транспортерній стрічці поступає через тічку в піч, що обертається. Просуваючись
по печі, глина піддається випаленню при температурі, близькій до спеканию. Обпалена глина
з печі подається в холодильник, в якому охолоджується до температури 150—180°
С. Затем шамот поступає на
пластинчатий транспортер, що подає його у вертикальний елеватор, і далі по
тічці прямує у витратний бункер або склад.
Печі для випалення глини на шамот, що обертаються,
як правило, працюють на твердому пилевугільному паливі.
Пальники і форсунки розташовуються в робочому об'ємі печей.
Для
дроблення обпаленого шамота застосовують щічні дробарки.
Обробка сировинних матеріалів
Глину, що поступає у виробництво, піддають первинному дробленню в
стругачах, каменевидних і дезінтеграторних вальцях, призначених також для
одночасного видалення з маси твердих включень.
При виготовленні виробів з напівсухою підготовкою маси після
первинного дроблення глину сушать і суху глину подрібнюють. Вибір необхідно
для цієї мети машини визначається властивостями глини (твердістю, вогкістю).
Для цієї мети застосовують бігуни сухого помелу, корзинчаті дезінтегратори.
Більш тонкий помел сухих порошків здійснюють в ротаційних і відцентрових
млинах.
При виготовленні виробів з пластичною підготовкою маси глину після
первинного дроблення проминають в бігунах мокрого помелу, глинорозтирачах, вальцях тонкого помелу.
Для отримання рідких мас у вигляді тонкомолотих суспензій (шлікеру) застосовують два
методи. В першому випадку непластичні матеріали подрібнюють до певної крупно
потім домелюють спільно з глинистим компонентом. За другим способом непластичн
матеріали піддають тонкому помелу і потім змішують з глинистою суспензією. При
цьому можна глину розпускати в агрегатах безперервної дії — роторних млинах, а
тонкий помел отощающих матеріалів
проводити у високопродуктивних струменевих млинах безперервного помелу.
Глиниста суспензія подається в басейни і сюди ж
дозують тонкомолоті порошки отощающих матеріалів.
Потім маса перемішується пропелерними мішалками і перекачується в басейни
готового шлікера, проходячи попутно
ситове очищення і магнітне збагачення.
Дроблення пластичних сировинних матеріалів
Первинне дроблення. Гвинтові камневидні вальці служать для дроблення рихлих глин і одночасного
виділення з них кам'янистих включень. Кінематична схема каменевидних вальців СМ-416 приведена на мал.
20.
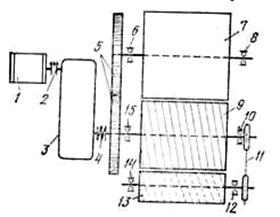
Мал. 20. Кінематична схема вальців: 1 — електродвигун, 2 — пружна
муфта, 3 — редуктор, 4 — зрівняльна муфта, 5 — зубчаті колеса, 6, 8, 10, 12, 14
15 — підшипники, 7 — гладкий вал, 9 — гвинтовий вал, 11 — ланцюгова передача,
13—очисний скребок
Від електродвигуна 1 через редуктор 3 обертання
передається зубчатим колесам 5, які передають обертання гладкому 7 і гвинтовому
9 валянням; ланцюгова передача 11 —очистному шкрябання 13.
Електродвигун сполучений з редуктором через пружну муфту 2, забезпечену
предохранительним пальцем, який необхідний у разі можливого заклинювання валів
при попаданні між .ними крупних твердих включень. В цьому випадку запобіжний
палець зрізається, обертання валів припиняється і цим запобігає аварії машини.
Гладкий і гвинтового валяння встановлюють на
пластинах, які кріплять до рами. На кінці гвинтового валу з боку приводу
шестерня із зубами, які дозволяють регулювати зазор між валяннями у міру їх
зносу за рахунок пересування гвинтового валу. Валяння цапфами спираються на
підшипники 6, 8, 10 і 15, встановлені в корпусах.
На валяннях є два очисні скребки: нерухомий,
очищаючий гладкий вал, і скребок 13, очищаючий гвинтовий вал. На гвинтовому
валу зроблена канавка для відкидання каміння в лоток, розташований між
корпусами підшипників 8— 10 в протилежній стороні від приводу. В місці виходу
каміння влаштований шарнірний клапан, який відкривається при попаданні в лоток
каменя.
Всі робочі органи вальців закриті кожухами, в
середній частині яких зроблена приймальна воронка, через яку подається глина.
Гвинтові каменевидні вальці забезпечуються амперметром, вказуючим навантаження
електродвигуна.
Технічна характеристика
гвинтових каменевидних вальців
СМ-416А
·
Продуктивність, м3/ч............................ 35
·
Розміри шматків, що виділяються, мм 35—180
·
Діаметр валів, мм...................... 400 і 500
·
Кутова швидкість, об/мин................... 92,7
·
Зазори між валяннями, мм ... 2 і 12
·
Габаритні розміри, мм:
·
довжина....................................................... 3100
·
ширина.................................................... 2000
·
висота 1200
·
Маса, т 2,5
Каменевидні (дезінтеграторні) вальці
Каменевидні (дезінтеграторні) вальці (мал. 21) служать для попереднього дроблення глин
часткового видалення кам'янистих включень, що грудкують. Вальці мають два вали
швидкохідний ребристий 2 і тихохідний гладкий 1.
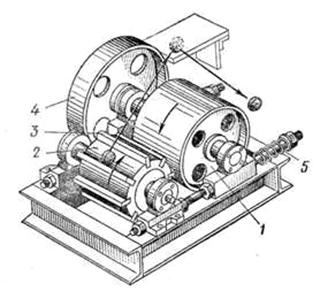
Мал. 21. Дезінтеграторні вальці: 1 і 2 —валки різного діаметра, 3 — подовжн
ребра, 4 — приводний шків, 5 — пружина
Глина поступає через завантажувальну воронку по
направляючому листу на швидкохідний ребристий вал. Під ударами ребер цього валу
вона відкидається на гладкий тихохідний вал, який затягує її в зазор між
валяннями. Кам'янисті включення, відскакуючи від гладкого валу, ударяються об
верхню кришку кожуха і викидаються через відвідний лоток.
Технічна характеристика
каменевидільних дезінтеграторних вальців
СМ-1198
·
Продуктивність, м3\ч......................................... 25
·
Габаритні розміри валів, мм:
·
діаметр швидкохідного валу .... 1000
·
діаметр тихохідного валу ............................... 600
·
Зазор між валяннями, мм 10
·
Кутова швидкість валів, об/мин...................400/40
·
Потужність електродвигуна, квт ..... 30
Продуктивність каменевидних вальців залежить від довжини
діаметра валів, числа їх оборотів і величини зазору між ними. Якщо виступи
ребристого валу притупляються, то припиняється відділення каміння. При появ
вироблень на гладкому валу відділення каміння утрудняє. В місцях вироблень в
гладкому і гвинтовому валяннях слід наварювати сталиніт з подальшою механічною
обробкою.
Перед пуском каменевидних вальців перевіряють: надійність
кріпильних деталей і скребків; зазори між скребками і валяннями; паралель осей
гладкого і гвинтового валів (непаралель, що допускається, 0,3 мм); зазор між
валяннями (повинен бути по виступах канавок не більше 2 мм, а по западинах — не
більше 12 мм); наявність мастила в підшипниках, редукторі і інших частинах, що
труть; справність сигналізації і інших запобіжних пристроїв. Зазор між
шкрябаннями і робочою поверхнею живлячого валу повинен бути в межах 0,5—1,5 мм.
Пускають вальці в такій послідовності. Спочатку включають транспортуючий
пристрій глини, розташований після вальців, потім електродвигун приводу вальців, а після того сак
валяння розвинуть необхідне число оборотів, приводять в дію пристрій, що пода
у вальці глину.
Під час роботи вальців слід спостерігати за їх рівномірним
завантаженням, періодично перевіряти ступінь нагріву підшипників, контролювати
розмір що виходять з машини шматочків глини і ступінь подрібнення матеріалу.
В процесі роботи вальців забороняється регулювати ширину щілини між валяннями, уручну
проштовхувати і видаляти шматки матеріалу із завантажувального отвору. При
заклинюванні валів слід негайно ж подати звуковий сигнал і вимкнути
електродвигун. Потім після вилучення електромонтером предохранителей валяння потрібно
повернути у зворотний бік і вийняти застряглі предмети. При проштовхуванн
застряглої між валяннями глини слід застосовувати дерев'яні пристосування.
Для зупинки вальців вимикають пристрій, що подає глину, і після
переробки всієї сировини, що знаходиться в завантажувальній воронці, вимикають
електродвигун вальців. Потім вимикають пристрої, за допомогою яких
транспортується масса після її обробки.
Для
раптової зупинки вальців дробильник повинен негайно подати сигнал про відключення
електродвигуна і після його зупинки повернути шків вальців у зворотний бік, що
б вивільнити їх від застряглих шматків матеріалу.
Причини неполадок при роботі каменевидних вальців
Причини неполадок при роботі каменевидних вальців і способи їх усунення приведен
в табл. 14.
Таблиця 14
Причини неполадок в каменевидільних вальцях
способи їх усунення
|
|
Неполадки |
Причини виникнення |
Способи усунення |
|
|
Зменшилася
продуктивність або припинився рух глини між валяннями або не обертаються
валяння |
На валяннях налипнула
глина |
Відрегулювати положення
скребка |
|
|
|
|
Глина зависла в тічці |
Очистити тічку від
глини |
|
|
Зрізають запобіжн
шпильки |
Поставити нові шпильки |
|
|
|
|
Заклінілісь валяння |
Поставити нові плавк
вставки в електрозахисті двигуна |
|
|
|
|
З'явився стукіт і шум збільшився |
Слабшали болтов
з'єднання |
Підтягти болти |
|
|
Пошкоджені підшипники |
Замінити підшипники |
|
|
Слабшали гайки на
стягнутих шпильках |
Підтягти гайки |
|
|
|
|
Перегріваються
підшипники |
Недостатньо змазан
частини, що труть |
Перевірити наявність
якість мастила |
|
|
Агрегат вібрує під час
роботи |
Ослаблено кріплення
машин на фундаменті |
Підтягти фундаментн
болти |
|
|
Не відрегульовано
положення вантажу на важелі клапана |
Відрегулювати положення
вантажу на важелі клапана |
|
|
Стругач складається з бункера, диска з ножами і приводу, що
обертається. Ножі диска при обертанні нарізують глину стружкою, яка
провалюється в передавальний лоток. Товщина стружки регулюється висуненням
ножів над поверхнею диска відповідно до вогкості глини. Величина шматків,
відбираних від стругача, повинна бути не більше 50 мм
Вторинне дроблення
Для вторинного дроблення глин застосовують бігуни і глинорозтирачі. Для проминки
розтирання глин, містить трудноразмокаємі у воді включення, з одночасним їх зволоженням застосовують
бігуни мокрого помелу. Для подрібнення сухих глин, що мають кар'єрну вогкість
не більше 12% або підсушених до вогкості менше 10%, застосовують бігуни сухого
помелу.
Бігуни залежно від пристрою можуть мати нерухомий або обертається
під. В першому випадку катки котяться по нерухомому череню при обертанні їх
осей навколо вертикального валу, а в другому випадку навкруги вертикальної осі обертається під,
а катки вертяться вільно навкруги своїх осей. В шпалери випадках подрібнення
здійснюється за рахунок власної тяжкості катків.
Принцип
роботи бігунів (мал. 22) наступний. Що поступає безперервно в чашу 2 бігунів
матеріал піддається раздавлюванню катками 3. Під
дією цих катків подрібнений матеріал продавлюється через отвори в плитах бігунів на тарілку, звідки скребком скидається
в лоток, стрічковий живильник або безпосередньо в стрічковий прес.
Технічн
характеристики бігунів приведені в табл. 15.
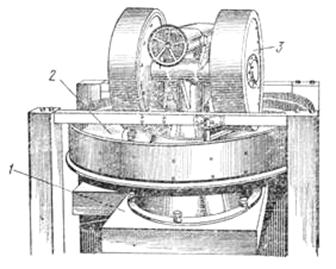
Мал. 22. Бігуни для мокрого помелу: 1 — підстава машини, 2
чаша, 3 — катки
Перед пуском бігунів слід перевірити: наявність
мастила на всіх частинах бігунів, що труть (підшипники фрикційної муфти
катків, вали, відомий шків, конічна зубчата передача, Повзуни напівосей катків
х направляючі); надійність закріплення захисних пристроїв на частинах
бігунів, що обертаються; справність заземлення металевих частин бігунів;
Надійність кріплення станини, бандажів до маточин катків, Пристроїв для подач
мастила, напівосей катків, корпуси чаші, опорних підшипників; справність
траверси і надійність підвіски в ній колінчастого валу, доріжок чаші,
кільцевого розвантажувального жолоба і скребків, приводу; герметичність огорож
катків; справність транспортних засобів, пов'язаних з бігунами, сіті, оглядових
завантажувальних люків, що водопідводить, пружинного затиску катків.
Таблиця 15
Технічн
характеристики бігунів
|
Показники |
Сухого помелу
|
Мокрого помелу
|
СМ-21
|
СМ-20
|
СМ-268
|
СМ-365
|
Продуктивність, м3/ч |
8,5* |
20* |
6-8* |
43* |
Розміри катків, мм |
1250X350 |
1800x550 |
1800x550 |
1800x800 |
Кутова швидкість чаші, об/мин |
23—27—30
|
18
|
|
22, 7
|
Потужність електродвигуна квт |
14,0 |
27,5 |
40 0 |
|
Габаритні розміри, мм
довжина
|
4350 |
6350 |
|
6700 |
ширина |
2918 |
3680 |
- |
3300 |
висота |
2870 |
3830 |
- |
4200 |
Маса т |
12,22 |
26,0 |
- |
31,6 |
* При подрібненні твердих матеріалів продуктивність бігунів в 2—3
рази нижче, ніж при подрібненні глин.
Обслуговування бігунів
Пуск бігунів проводиться наступним шляхом. Спочатку пускають
відбірковий транспорт, потім бігуни і після того, як його катки, що
обертаються, набирають повне число оборотів, починають живлення бігунів
сировиною.
Під час роботи бігунів необхідно стежити: за рівномірною
безперервною подачею матеріалу в бігуни; відсутністю сторонніх предметів;
станом кріпильних деталей; роботою катків і скребків; станом матеріалу, що
розмелюється, на черені; роботою всіх механізмів бігунів (повинні працювати без
вібрацій, скрипу, поштовхів і зайвого шуму) і транспортних засобів, пов'язаних
з бігунами; станом мастила і роботою підшипників (їх корпуси не повинн
нагріватися більш ніж до 60°, що перевіряється навпомацки); чистотою всіх
механізмів бігунів; справністю приводу, фрикційної муфти і огорож;
герметичністю кожуха і справністю пружинних затисків катків.
Під час роботи бігунів забороняється: знімати огорожі з їх частин,
що обертаються; витягувати з чаші негабаритні шматки матеріалу або по сторонн
предмети; проводити ремонтні і налагоджувальні роботи, чищення і мастило механізмів;
підгрібати і розрівнювати матеріал, що розмелюється.
Проби розмолотого матеріалу слід відбирати тільки з
розвантажувальних тічок бігунів.
Під час роботи бігунів необхідно стежити за розмірами шматків
глини, які не повинні перевищувати 90—100 мм; не допускати завалів або перебою
в живленні машини. Товщина шару під катками не повинна перевищувати 30—40 мм
Ступінь зволоження визначають по зовнішніх ознаках: нормально
оброблена і зволожена глина не прилипає до катків і шкрябань і має вид маси, що
складається з невеликих грудочок. Недостатньо зволожена глина складається з не
злиплих між собою шматочків неоднакової вогкості, які при розминц
розсипаються. Перезволожена глина прилипає до катків, замазує отвори і стіни
чаші.
Зупинка бігунів допускається тільки в наступних
випадках: при появі в агрегаті незвичайного шуму, стукоту або вібрації; при
перегріві електродвигуна і підшипників, що визначається по специфічному запаху
гару і появі диму; при поломці механізмів бігунів, захисних і сигналізуючих
пристроїв; виявленні несправності ізоляції електроапаратури, що виявляється в
«битті на корпус» у момент дотику до металевих частин агрегату; при
необхідності регулювання механізмів бігунів; порушенні герметичності кожуха, що
видно з підвищеного виділення пилу; при тимчасовій перерві в подач
електроенергії і відсутності обслуговуючого персоналу; загрозі або виникненн
аварії; необхідності мастила, огляду, очищення і дрібного ремонту механізмів
бігунів; при припиненні дії завантажувальних і відбіркових пристроїв. Зупинка
бігунів відбувається таким чином. Припиняють подачу матеріалу в завантажувальну
воронку і після повного вироблення матеріалу вимикають пусковий пристрій
бігунів. Після повної зупинки вимикають відбірковий пристрій.
Після закінчення роботи бігуни звільняють від глини, а вс
завантажувальні і розвантажувальні пристосування і отвори в плитах прочищають.
Дірчасті вальці
Дірчасті вальці замінюють бігуни, особливо якщо глина заздалегідь
подрібнювалася і зволожувалася. У валяннях дірчастих вальців є отвори, через як
продавлюється глина.
Таблиця 16
Технічн
характеристики дірчастих вальців
|
СМ-369А
|
СМ-927
|
Продуктивність, т/ч |
До 40 |
До 75 |
Зазор між валяннями, мм |
5—10 |
5—10 |
Діаметр валів, мм |
1000 |
1012 |
Ширина валів, мм |
600 |
640 |
Кутова швидкість, об/мин: |
30 |
30,8 |
відомого валу |
|
|
провідного валу |
20,8 |
25,5 |
|
|
|
|
Продуктивність дірчастих вальців залежить від ступеня зволоження і пластичності маси,
розмірів і форми отворів, через які продавлюється маса, і числа оборотів валів.
Перед початком роботи слід перевірити справність пружинних
притискних пристроїв у підшипників рухомого відомого валу; величину зазору між
валяннями і відрегулювати його за допомогою гвинтового упора; переконатися у
відсутності тріщин на валяннях; наявності і справності захисних огорож.
Подавати глину в завантажувальний отвір слід тільки після
досягнення валяннями постійної швидкості обертання.
Необхідно стежити за рівномірним завантаженням вальців глиною,
нормальною роботою валів і пружинного притискного пристрою, станом
регулювальних гвинтів і гайок, наполегливих гвинтових пристроїв; мастилом підшипників
валів. Причини виникнення несправностей дірчастих вальців і способи їх усунення
приведені в табл. 17.
Таблиця 17
Неполадки при роботі дірчастих вальцов і способи їх усунення
|
Неполадки
|
Причини виникнення
|
Способи усунення
|
|
Зменшення продуктивност
вальців
Перегрів підшипників
|
На валяння налипа
глина Зносилися робочі поверхні валів Засмітилися отвори у валяннях
Недостатня кількість мастила або забруднення
|
Зменшити вогкість матеріалу Проточити валяння
Прочистити отвори Перевірити мастило
|
|
Тонке подрібнення глин
Для тонкого подрібнення глин, що пройшли попередн
подрібнення на бігунах або вальцях грубого помелу, застосовують диференціальн
гладкі вальці тонкого помелу (мал. 25).
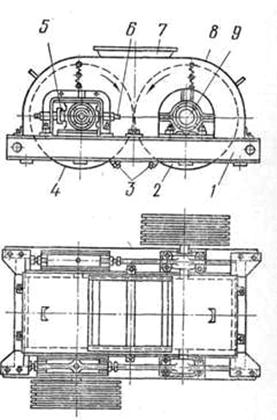
Мал. 25. Вальці тонкого помелу: 1 — станина, 2, 4 — валяння,
3 — скребок, .5— амортизація, 6 — регулювальний гвинт, 7— завантажувальна
воронка, 8 — кожух, 9 — підшипникові опори
Матеріал через завантажувальну воронку 7
поступає між валяннями 4 і 2, мають різну швидкість, і роздавлюється ними.
Очищення валів від налипаючої глини проводиться скребком 3. Вал забезпечений
амортизацією 5 і гвинтом 6 для регулювання зазора між валяннями. Валяння
встановлені в підшипникові опори 9, укріплені на станині.
Продуктивність диференціальних гладких вальців тонкого помелу залежить
від їх довжини і діаметра, а також від числа оборотів валів. На заводах
будівельної кераміки застосовують вальці тонкого помелу СМ-23, СМ-24, СМ-696А.
Технічн
характеристики диференціальних вальців
тонкого помелу
|
СМ-696А
|
СМК-102
|
Продуктивність, м3/ч |
18 |
25 |
Розмір завантажуваних шматків, мм
|
До 300 |
До 300 |
Габаритні розміри валів, мм:
|
|
|
діаметр |
800 |
1000 |
довжина |
600 |
1000 |
Зазор між валяннями, мм
|
До 2 |
До 1 |
Габаритні розміри, мм:
|
|
|
довжина |
3240 |
5300 |
ширина |
2515 |
3300 |
висота |
965 |
2100 |
Кутова швидкість, об/мин |
100/180 |
290/145 |
Потужність електродвигуна, квт |
24 |
55 |
Маса, т |
2,4 |
13 |
В даний час освоюється виробництво вальців СМК-102
тонкого помелу з гладкими валяннями і шліфуючим пристроєм.
Обслуговування вальців тонкого помелу аналогічно
обслуговуванню каменевидільних вальців. При появі між валяннями зазора більше
3 мм їх наварюють сталінітом.
Для зміни зазора слід ослабити контргайки, гвинтами
встановити необхідний зазор і знов затягнути контргайки.
Таблиця 18
Неполадки у вальцях СМ-696А і способи їх усунення
|
Неполадки
|
Причини виникнення
|
Способи усунення
|
|
Зменшення продуктивності |
Маса налипає на валах |
Очистити вали і скребки |
|
Слабо натягнуті приводні ремені |
Натягнути приводні ремені |
|
Поступають велик
шматки для дроблення |
Зменшити розмір шматків,
що поступають |
|
Зрізалися шпонки шківа
або вилки |
Замінити шпонки |
|
Поява стукоту |
Пошкоджені підшипники |
Замінити підшипники |
|
Ослаблені болтов
з'єднання |
Підтягти болтов
з'єднання |
|
Підшипники перегріваються |
Недостатньо змазан
частини, що труть |
Перевірити наявність
якість мастила |
|
Пошкоджені підшипники |
Замінити підшипники |
|
Зносилися зуби
шестерень |
Замінити шестерні |
|
Перед пуском вальців перевіряють стан болтових з'єднань, наявність
масла в підшипниках, величину зазора між валяннями, силу натягнення гумових
амортизацій, правильність установки скребків.
Неполадки в роботі вальців і способи їх усунення приведені в табл. 18.
Подрібнення сухих глин. Найефективнішими
машинами для подрібнення сухих глин є бігуни сухого помелу і корзинчат
дезінтегратори. Дезінтегратори служать для тонкого подрібнення підсушених
пластичних матеріалів і розбивання грудок зволожених порошкоподібних мас.
Дроблення непластичних сировинних матеріалів
Для грубого дроблення бою виробів, шлаку і вугілля перед
помелом і в окремих випадках сланцевих глин застосовують щокові дробарки.
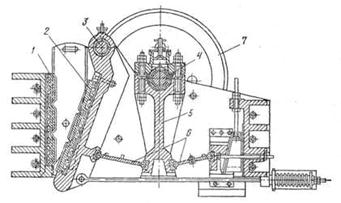
Мал. 26. Щокова дробарка Щ-5: 1 — нерухома щока, 2 —подвижна
щока, 3 — шарнір, 4 — ексцентриковий вал, 5 — шатун, 6 — плити розпорів, 7
маховик
Щічні дробарки підрозділяються: по характеру підвіски
рухомої щоки — з верхнім і нижнім підвісом; по характеру руху підвісної щоки
з простим і складним рухом; по конструкції механізму, що передає рух рухомо
щоки, — з механізмами шарнірно-важеля, роликового або ексцентрикового.
Працює щічна дробарка (мал. 26) таким чином. Шматки
матеріалу завантажуються між нерухомою щокою 1 і рухомої 2. Рухома щока за
допомогою валу 4 обертається навкруги шарніра. Матеріал роздавлюється
висипається через отвір. Ступінь подрібнення матеріалу регулюють зміною ширини
вихідної щілини за допомогою клинів.
Продуктивність щічної дробарки залежить головним чином від
ширини розвантажувального отвору, ширини щоки, величини відходу рухомої щоки
числа оборотів ексцентрикового валу. Залежно від необхідності отримання
матеріалу тієї або іншої крупної встановлюється ширина розвантажувального
отвору.
Література
1. Борщевский А.А.,
Ильин И.С., Механічної устаткування підприємств будівельної індустрії. М.
Висш. школа,1986
2. Сапожников М.Я.,
Дроздов Н.Е. Довідник по устаткуванню заводів будівельних матеріалів. М., 1970
3. Константопуло Г.С.
Приклади і задачі по механічному устаткуванню підприємств збірного залізобетону.,
М., Висш. школа, 1984.
|