Учебное пособие: Госстандарт России по электрооборудованию
4.1.7
Двигатели должны обеспечивать номинальную нагрузку при температуре охлаждающей
воды от 1 до 33 °С.
4.1.8
Номинальные значения кратности начального пускового, минимального и максимального
моментов и начального пускового тока двигателей должны соответствовать ГОСТ
9630. При этом минимальное значение кратности максимального момента двигателей
для привода насосов должно быть не менее 2,0 о. е.
Для
двигателей трактов топливоприготовления и топливоподачи значения кратности
пускового и максимального моментов должны соответственно составлять не менее
1,4 и 2,5 о. е., при этом кратности начальных пусковых токов могут превышать
значения, приведенные в ГОСТ 9630.
4.1.9
Номинальные значения коэффициента полезного действия и коэффициента мощности
должны быть установлены в технических условиях на двигатели конкретных типов.
4.1.10
Двигатели должны выдерживать прямой пуск от полного напряжения сети и
обеспечивать пуск механизма как при номинальном напряжении сети, так и при
напряжении не менее 80 % номинального в процессе пуска.
В
технически обоснованных случаях допускается по согласованию устанавливать более
низкое значение напряжения, но не менее 75 % номинального для наиболее мощных
двигателей.
Значения
моментов сопротивления на валу двигателей при пусках, а также допустимых
моментов инерции приводимых механизмов должны быть установлены в технических
условиях на двигатели конкретных типов.
4.1.11
Двигатели должны обеспечивать:
- два
пуска подряд из практически холодного состояния;
- один
пуск из горячего состояния;
-
последующие пуски через 3 ч.
4.1.12
Двигатели должны быть рассчитаны на 10000 пусков за срок службы (при мощности
до 5000 кВт включительно) или 7500 пусков (при мощности двигателя более 5000
кВт).
4.1.13 В
пределах числа пусков по 4.1.12 двигатели должны допускать до шести пусков за
сутки (при пусконаладочных работах — до восьми пусков за сутки), а за год:
-
насосная группа механизмов — 300—800 пусков;
-
питательные насосы — 400—700 пусков;
-
тягодутьевые механизмы — 500—700 пусков;
-
механизмы топливоприготовления — 800—1000 пусков;
-
механизмы топливоподачи — до 2500 пусков, при этом меньшие значения
относятся к двигателям мощностью более 5000 кВт.
4.1.14
Вертикальные двигатели, воспринимающие осевую нагрузку на вал, должны
соответствовать требованиям 4.1.12 и 4.1.13 при условии замены деталей
подшипниковых узлов с периодичностью, указанной в инструкции изготовителя.
4.1.15
Пуск двухскоростных двигателей до большей частоты вращения должен происходить
ступенчато через меньшую частоту вращения. В случае необходимости
двухскоростные двигатели должны допускать бесступенчатый пуск до большей
частоты вращения. Число таких пусков должно быть указано в технических условиях
на конкретные двигатели.
Коммутация
таких двигателей должна производиться не более чем двумя выключателями.
4.1.16
Двухскоростные двигатели должны допускать шесть переключений схемы соединений
обмотки статора (изменений частоты вращения) в сутки.
4.1.17
По условиям крепления обмотки статора двигатели должны допускать повторную
подачу питания при векторной сумме остаточного напряжения на шинах собственных
нужд, к которым подключен двигатель, и вновь подводимого напряжения питания, не
превышающего 180 % номинального.
Двухскоростные
двигатели, работающие на большей частоте вращения, при повторной подаче
напряжения должны обеспечивать самозапуск на той же частоте вращения.
Количество
режимов с повторной подачей питания за срок службы двигателя — не более 500.
4.1.18
Двигатели должны изготовляться с подшипниками качения или скольжения.
Тип
смазки подшипников — по ГОСТ 9630.
Подшипники
должны быть оснащены датчиками теплоконтроля.
Двигатели
мощностью 630 кВт и более, предназначенные для эксплуатации в тяжелых условиях
(углеразмольные механизмы, дымососы и т. п.), по согласованию должны быть
оснащены датчиками вибрации подшипников.
4.1.19
.Подшипники скольжения с принудительной смазкой под давлением должны работать
при температуре подаваемой смазки от 30 до 45 °С. При прекращении подачи смазки подшипники должны
допускать работу не менее 2 мин с номинальной частотой вращения и в дальнейшем
на выбеге агрегата при согласованных режимах.
4.1.20
Для двигателей с принудительной смазкой подшипников должна быть предусмотрена
возможность использования для смазки негорючей жидкости.
4.1.21 В
двигателях должен быть предусмотрен тепловой контроль обмотки и сердечника
статора, охлаждающего, воздуха и охлаждающей воды на входе и выходе из
воздухоохладителя в соответствии с ГОСТ 9630.
4.1.22
Двигатели мощностью 3000 кВт и более должны иметь схему обмотки «звезда» и
встроенные трансформаторы тока для дифференциальной защиты, которые выбираются
по номинальному значению тока статора.
4.1.23
Допустимые вибрации двигателей — по ГОСТ 20815.
4.1.24
Допустимые уровни шума односкоростных двигателей — по ГОСТ 16372, а
двухскоростных двигателей — по ГОСТ 16372 и техническим условиям на двигатели
конкретных типов.
4.1.25
Номенклатура и значения показателей надежности должны быть указаны в
технических условиях на двигатели конкретных типов, включая:
- срок
службы до капитального ремонта — восемь лет;
-
расчетный срок службы подшипников качения — не менее 20000 ч — для двухполюсных
двигателей, 30000 ч — для вертикальных двигателей и не менее 50000 ч — для
остальных типов двигателей.
4.1.26
Комплектность двигателей — по стандартам и техническим условиям на двигатели
конкретных типов, включая ремонтную документацию по ГОСТ 2.602.
В
комплект поставки двигателя с принудительной смазкой подшипников должна входить
маслостанция, если для подшипников приводимого механизма принудительной смазки
не требуется.
4.1.27
Маркировка двигателей — по ГОСТ 26772 и техническим условиям на двигатели
конкретных ТИПОВ.
4.1.28
Упаковка двигателей — по ГОСТ 23216 и техническим условиям на двигатели конкретных
типов.
4.2
Требования к конструкции двигателей
4.2.1
Класс нагревостойкости электроизоляционных материалов, применяемых в
двигателях, должен быть не ниже В по ГОСТ 8865.
4.2.2
Выводные устройства двигателей должны быть изготовлены в соответствии с
требованиями ГОСТ 9630.
Обмотка
статора двигателей должна иметь шесть выводных концов, закрепленных в выводном
устройстве: три конца являются выводами трех фаз, а остальные три конца
соединяются вместе в нулевую точку. По согласованию соединение выводных концов
в нулевую точку может выполняться в отдельной коробке.
4.2.3
Двухскоростные двигатели должны быть оснащены вводными устройствами для каждой
частоты вращения.
4.2.4
Класс нагревостойкости изоляции выводных концов должен соответствовать классу
нагревостойкости изоляции обмотки статора.
4.2.5
Конструкция выводного устройства должна обеспечивать возможность подключения и
уплотнения одного или двух трехжильных питающих кабелей с медными или
алюминиевыми жилами. В технически обоснованных случаях по согласованию
конструкция выводного устройства должна обеспечивать подключение и уплотнение
трех и более трехжильных питающих кабелей.
4.2.6
Двигатели, оснащенные встроенными трансформаторами тока для дифференциальной
защиты, должны иметь два выводных устройства: одно — для вывода начала фаз
обмотки статора, а второе — для вывода концов обмотки статора, образующих
нулевую точку.
4.2.7
Выводные устройства должны допускать разворот с фиксацией через 90° для подвода
питающих кабелей с любой стороны. По согласованию выводные устройства
двигателей мощностью более 2500 кВт могут допускать разворот с фиксацией через
180°.
4.2.8
Элементы конструкции выводного устройства при токе короткого замыкания 40 кА
длительностью 0,5 с и при ударном токе 128 кА не должны разрушаться до степени,
угрожающей безопасности обслуживающего персонала.
4.2.9
Выводные устройства должны допускать отгибание отсоединенных кабелей вместе с
узлом крепления на период испытаний.
4.2.10
Подшипниковые узлы двигателей должны соответствовать требованиям ГОСТ 9630.
Конструкция лабиринтовых уплотнений подшипника должна исключать вытекание
жидкой смазки из корпуса подшипника.
4.2.11
Стояковые подшипники скольжения двигателей должны быть установлены на единую
фундаментную плиту двигателя.
Стояковые
подшипники двигателей мощностью более 1000 кВт должны быть изолированы от
фундаментной плиты и маслопроводов со стороны, противоположной присоединенному
механизму.
4.2.12
Двигатели не должны иметь вентиляционных устройств с автономным электропитанием
(«вентиляторов—наездников»).
4.2.13
Двигатели мощностью более 1000 кВт климатического исполнения У, УХЛ, О, Т и
способа охлаждения ICA01A61 или IGA01A51 в технически обоснованных случаях по
согласованию должны быть оснащены встроенными электронагревателями, собранными
из групп однофазных нагревателей на 220 В, подключенных к сети напряжением 380
В. Зажимы нагревателей должны быть выведены на клеммную сборку; изоляция
проводки нагревателей не должна поддерживать горение.
Конструкция
корпуса должна обеспечивать удобство монтажа и демонтажа нагревателей и защиту
персонала от случайного прикосновения.
4.2.14
Двигатели со встроенными водяными воздухоохладителями должны иметь конструкцию,
обеспечивающую их работоспособность в случае протекания воды из
воздухоохладителя, и должны быть оснащены датчиком наличия воды в корпусе.
Рабочее
давление воды в воздухоохладителях должно быть не более 600 кПа.
4.2.15
Двигатели должны быть оснащены дренажным отверстием для отвода конденсата и
утечек воды, конструкция которого по степени защиты должна соответствовать ГОСТ
17494.
4.2.16
Соединение двигателей горизонтального исполнения с приводимым механизмом — с
помощью муфты, не передающей осевые усилия на вал двигателя. Значения
радиальных усилий должны быть установлены в технических условиях на двигатели
конкретных типов.
Двигатели
вертикального исполнения с фланцевым соединением с приводимым механизмом должны
выдерживать осевые и радиальные усилия на валу, передаваемые механизмом, и
кратковременное вращение двигателя в обратном направлении. Значения усилий и
условия перехода на обратное направление вращения должны быть установлены в
технических условиях на конкретные типы двигателей.
5
Требования безопасности
Двигатели
должны соответствовать требованиям безопасности ГОСТ 12.2.007.0, ГОСТ 12.2.007.1,
ГОСТ 12.1.003, ГОСТ 9630 и [1].
6
Правила приемки
6.1 Для
проверки соответствия двигателей требованиям настоящего стандарта проводят
приемочные, квалификационные, приемосдаточные, сертификационные, периодические
и типовые испытания.
Приемочные,
квалификационные, приемосдаточные, периодические и типовые испытания двигателей
должен проводить изготовитель по ГОСТ 183, ГОСТ 9630 и настоящему стандарту.
Сертификационные
испытания двигателей должен проводить испытательный центр (лаборатория),
аккредитованный на право; проведения указанных испытаний в установленном
порядке.
В случае
невозможности проведения части, испытаний на стенде изготовителя эти испытания
должны проводиться на месте установки двигателя изготовителем.
6.2
Приемочные испытания проводят на опытном (головном) образце двигателя в
следующем объеме.
6.2.1
Испытания по программе приемочных согласно ГОСТ 9630.
6.2.2
Проверка возможности прямого пуска двигателя от сети
6.2.3
Проверка возможности бесступенчатого пуска двухскоростного двигателя от сети до
большей частоты вращения.
6.2.4
Проверка работоспособности подшипниковых узлов скольжения с принудительной
смазкой под давлением.
6.2.5
Измерение перепада давления воды в встроенном воздухоохладителе двигателя с
замкнутой системой охлаждения.
6.2.6 Испытания
на электромагнитную совместимость, т. е. на устойчивость к воздействию
электромагнитных помех следующих видов: отклонение напряжения, отклонение
частоты, одновременное отклонение напряжения и частоты от номинальных значений,
несимметрия и несинусоидальность напряжения питающей сети.
6.2.7
Ресурсные испытания двигателя или его отдельных узлов для определения их
работоспособности.
6.3
Приемосдаточные испытания проводят по ГОСТ 9630 в следующем объеме.
6.3.1
Испытания по программе приемосдаточных согласно ГОСТ 9630.
6.3.2
Определение уровня шума.
6.3.3
Проверка целостности воздухоохладителей.
6.4
Квалификационные испытания проводят по ГОСТ.9630 и 6.2 настоящего: стандарта.
6.5
Сертификационные испытания рекомендуется проводить на головном образце двигателя
или на типопредставителях серийно выпускаемых двигателей по согласованной
программе.
6.6
Периодические испытания проводят на одном двигателе из числа прошедших
приемосдаточные испытания не реже одного раза в три года по программе
периодических испытаний по ГОСТ 9630 и 6.2 настоящего стандарта, за исключением
проверки безопасности выводного устройства и ресурсных испытаний.
6.7
Типовые испытания двигателя проводят по ГОСТ 9630.
7
Методы испытаний
7.1
Методы испытаний двигателей - по ГОСТ 183, ГОСТ 9630, ГОСТ 11828 и ГОСТ 7217 и
настоящему стандарту.
7.2
Оценку надежности двигателей проводят один раз в три года по показателям
надежности двигателей каждого типоисполнения, полученным путем сбора и
статистической обработки данных двигателей, находящихся в эксплуатации, в
соответствии с нормативной документацией, утвержденной в установленном порядке.
Количество контролируемых двигателей каждого типоисполнения устанавливают по
согласованию.
7.3
Проверку возможности прямого пуска двигателя от сети проводят с подсоединенным
к двигателю механизмом или маховой массой на валу, соответствующей допустимой
маховой массе приводимого механизма. Напряжение при пуске должно
соответствовать указанному в 4.1.10.
7.4
Проверку возможности бесступенчатого пуска двухскоростного двигателя до большей
частоты вращения проводят путем пуска от сети аналогично 7.3 при схеме
соединения обмотки статора двигателя, соответствующей большей частоте вращения.
7.5
Водяной воздухоохладитель испытывают давлением 1,5 Рраб
(рабочего давления) в течение 15 мин.
Перепад
давления воды в воздухоохладителе и расход воды определяют при помощи манометра
и расходомера соответственно.
7.6
Испытания подшипников скольжения с принудительной смазкой под давлением
проводят при номинальном расходе масла и при прекращении подачи масла после
достижения подшипниками установившейся температуры. В течение 2 мин после
прекращения подачи масла и за время выбега двигателя температура вкладышей
подшипников не должна превышать предельно допустимой по ГОСТ 183.
7.7
Ресурсные испытания двигателя на допустимое число пусков проводят на одном
типопредставителе серии путем пусков двигателя с маховой массой,
соответствующей допустимой маховой массе приводимого механизма, по методике,
согласованной между изготовителем и потребителем.
7.8
Испытание выводного устройства двигателя на безопасность проводят по методике,
согласованной между изготовителем и потребителем.
7.9
Проверку двигателя на устойчивость к воздействию электромагнитных помех
проводят по методике, согласованной между изготовителем и потребителем.
7.10
Соответствие двигателей требованиям стойкости к механическим внешним
воздействующим факторам и сейсмостойкости должно быть подтверждено расчетами по
ГОСТ 17516.1.
8
Транспортирование и хранение
Транспортирование
и хранение двигателей — по ГОСТ 23216 и техническим условиям на двигатели
конкретных типов.
9
Указания по эксплуатации
9.1
Условия эксплуатации двигателей — по настоящему стандарту, правилам [2], [3], а
также по техническим условиям и инструкции по эксплуатации по ГОСТ 2.601 на
двигатели конкретных типов.
9.2
Заказчик должен обеспечить эффективную защиту двигателей от многофазных
коротких замыканий, неполнофазных режимов, оттоков перегрузки (перегревов),
затяжных пусков, перерывов в подаче охлаждающей воды и масла, а также
эффективный контроль за тепловым и вибрационным состоянием двигателей по
датчикам, установленным изготовителем в соответствии с [2].
Поставляемые
с двигателем датчики должны быть пригодны для подключения к автоматическим
системам контроля и диагностики.
9.3 При
отсутствии разгона двигателя с присоединенным механизмом до установившейся
частоты вращения двигатель должен быть отключен от сети защитой:
не более
чем через 5 с после включения в случае двухполюсного двигателя;
не более
чем через 10 с после включения во всех остальных случаях.
9.4
Двигатели с замкнутой системой вентиляции и встроенными водяными
воздухоохладителями должны иметь защиту, действующую на сигнал, при уменьшении
потока воды ниже заданного значения и на отключение двигателя, при его
прекращении. Кроме того, должна быть предусмотрена сигнализация, действующая
при появлении воды в корпусе двигателя.
Водяные
воздухоохладители должны быть рассчитаны на нормальную работу при использовании
пресной, минеральной и морской воды.
9.5
Вибрация подшипников двигателя, соединенного с механизмом, должна
соответствовать требованиям [2].
10
Гарантии изготовителя
10.1
Изготовитель должен гарантировать соответствие двигателя требованиям настоящего
стандарта и технических условий на конкретные виды двигателей при условии
соблюдения правил транспортирования, хранения, монтажа и эксплуатации.
10.2
Гарантийный срок — три года с начала эксплуатации двигателя.
Гарантийный
срок эксплуатации исчисляется со дня ввода двигателя в эксплуатацию, но не
позднее 6 мес для действующих и 9 мес для строящихся объектов со дня
поступления к заказчику (потребителю).
ГОСТ Р МЭК 332-1-96
УДК
621.315.2.001.4:006.354 Группа Е46
ГОСУДАРСТВЕННЫЙ СТАНДАРТ
РОССИЙСКОЙ ФЕДЕРАЦИИ
ИСПЫТАНИЯ КАБЕЛЕЙ НА
НЕРАСПРОСТРАНЕНИЕ ГОРЕНИЯ
Испытание одиночного
вертикально расположенного изолированного провода или кабеля
Fest of cables
under fire conditions. Fest of a single vertical insulated wire or cable
ОКС 29.060.20
ОКСТУ 3509
Дата введения
1997-01-01
Предисловие
1 РАЗРАБОТАН И ВНЕСЕН
Техническим комитетом ТК 46 "Кабельные изделия" при АО Всероссийский
научно-исследовательский, проектно-конструкторский и технологический институт
кабельной промышленности" (АО ВНИИКП) Росскоммаша
ПРИНЯТ И ВВЕДЕН В
ДЕЙСТВИЕ Постановлением Госстандарта России от 8 апреля 1996 г. № 258
2 Настоящий стандарт
представляет собой аутентичный текст МЭК 332-1-93 "Испытания кабелей на
нераспространение горения. Испытание одиночного вертикально расположенного
изолированного провода или кабеля"
3 ВВЕДЕН ВПЕРВЫЕ
1 ОБЩИЕ ПОЛОЖЕНИЯ
1.1 Область применения
Настоящий стандарт
устанавливает метод испытания одиночного вертикально расположенного
изолированного провода или кабеля на нераспространение горения и требования к
оценке результатов испытания.
Примечания
1 Применение провода или
кабеля, не распространяющего горение в соответствии с требованиями настоящего
стандарта, не гарантирует предотвращение распространения огня при всех способах
его прокладки, поэтому в тех случаях, когда риск распространения огня велик,
например, при высоких вертикальных пучках кабелей, следует принимать
дополнительные меры предосторожности. Если одиночный образец кабеля
соответствует требованиям настоящего стандарта, то нельзя делать вывод, что
этот кабель в пучках не будет распространять горение.
2 Приведенный метод не
применим для испытания проводов небольших размеров (с жилами диаметром менее
0,8 мм или сечением менее 0,5 мм2 ) из-за возможности плавления
токопроводящей жилы до окончания испытания.
2 НОРМАТИВНЫЕ ССЫЛКИ
В настоящем стандарте
использована ссылка на МЭК 695—2—4/1, 1991 Испытания на пожаробезопасность.
Часть 2. Методы испытаний. Раздел 4. Лист. 1. Газовая горелка номинальной
мощностью 1 кВт с предварительным смешением газов и указания по эксплуатации.
3 ОБРАЗЕЦ
Образец представляет
собой отрезок провода или кабеля длиной (600 ± 25) мм.
4 КОНДИЦИОНИРОВАНИЕ
Перед испытанием образцы
выдерживают не менее 16 ч при температуре (23 ± 5) °С и относительной влажности (50 ± 20)
%.
Если провод или кабель
покрыт краской или лаком, перед кондиционированием образец выдерживают в
течение 4 ч при температуре (60 ± 2)°С.
5 ИСПЫТАТЕЛЬНОЕ
ОБОРУДОВАНИЕ
Испытательная камера и
расположение образца показаны на рисунках 1 и 2, приведенных в приложении А.
Испытательную камеру
размещают в помещении, в котором нет сквозняков, но имеются системы удаления
токсичных газов, выделяемых при горении. В помещении, где проводятся испытания,
должна поддерживаться температура (23 ± 10) °С.
Примечания
1 Если в качестве
закрытого помещения используют обычный вытяжной шкаф, то он должен иметь
устройство отключения, позволяющее работать при выключенном вытяжном
вентиляторе. Некоторые вытяжные шкафы оборудуют таким устройством.
2 Если в качестве места
для проведения испытания используют вытяжной шкаф, рекомендуются следующие
операции, обеспечивающие безопасность работы:
а) выключить вытяжной
вентилятор, наглухо закрыть выходное отверстие;
б) опустить переднюю
дверцу вытяжного шкафа, оставив такой зазор, чтобы можно было установить
горелку в требуемом положении;
в) убедиться в
безопасности работы оператора;
г) не перемещать дверцу
вытяжного шкафа во время испытания;
д) в конце испытания
перед открытием дверцы вытяжной шкаф следует полностью проветрить.
6 РАСПОЛОЖЕНИЕ ОБРАЗЦА
Образец должен быть
закреплен вертикально в двух местах и установлен в трехстенной, без передней
стенки металлической камере высотой (1200 ± 25) мм, шириной (300 ± 25) мм и
длиной (450 ± 25) мм; верх и дно камеры должны быть закрытыми.
Образец закрепляют при
помощи медной проволоки сечением 1 мм2 к двум горизонтальным опорам
так, чтобы расстояние между нижним краем верхней опоры и верхним краем нижней
опоры составляло (550 ± 5) мм. Кроме того, образец должен быть расположен так,
чтобы его нижний конец находился на расстоянии около 50 мм от дна камеры.
7 ИСТОЧНИК
ВОСПЛАМЕНЕНИЯ
Источником воспламенения
является газовая горелка, соответствующая требованиям стандарта МЭК 695—2—4/1,
в котором также приведен метод проверки и регулировки пламени.
8 ПРОВЕДЕНИЕ ИСПЫТАНИЯ
Меры безопасности
Необходимо принять меры,
чтобы обезопасить персонал и в процессе проведения испытаний не допустить:
а) возникновения пожара
или взрыва;
б) вдыхания дыма и/или
токсичных продуктов, особенно если горят галогенные материалы;
в) контакта с токсичными
остатками сгорания.
8.1 Воздействие пламени
Откалиброванную горелку,
соответствующую разделу 7, включают и устанавливают требуемые скорости потока
газа и воздуха. Горелка должна быть расположена так, чтобы кончик внутреннего
конуса пламени синего цвета касался поверхности образца на расстоянии (475 ± 5)
мм от нижнего края верхней горизонтальной опоры, при этом ось сопла горелки
должна быть под углом 45° к вертикальной оси образца (см. рисунок 3,
приведенный в приложении А).
Место воздействия пламени
для плоских кабелей должно быть в средней части плоской стороны кабеля.
В конце испытания горелку
удаляют, а пламя горелки гасят.
8.2 Время воздействия
пламени
Пламя должно действовать
на образец непрерывно в течение времени, зависящего от диаметра образца, в
соответствии с указанным в таблице 1.
Таблица 1
Наружный диаметр*
образца, мм |
Время воздействия
пламени, с |
D<25 |
60 |
25 < D
£ 50
|
120 |
50 < D
£ 75
|
240 |
D<75 |
480 |
________
* При испытании кабелей
некрупного сечения (например, плоских кабелей) определяют периметр кабеля и
рассчитывают эквивалентный диаметр круглого кабеля.
Примечание — Для плоских
кабелей, имеющих соотношение большой и малой осей более 17:1, значения времени
воздействия пламени находятся в стадии рассмотрения.
8.3 Оценка результатов
После того как горение
полностью прекратится, образец тщательно протирают тканью.
Допускается на
поверхности образца после протирки наличие сажи, если поверхность образца
осталась без повреждений. Размягчение или какую-либо деформацию
неметаллического материала также не учитывают. Расстояние от нижнего края
верхней опоры до начала обугленной части образца измеряют с точностью до 1 мм.
Начало обугленной части
определяют следующим образом. На поверхность кабеля нажимают острым предметом,
например лезвием ножа. Место, где фиксируется изменение упругой поверхности
образца на хрупкую (крошащуюся), считают началом обугленной части.
9 НОРМИРУЕМЫЕ ЗНАЧЕНИЯ
Провод или кабель считают
выдержавшим испытание, если расстояние от нижнего края верхней опоры до начала
обугленной части более 50 мм.
Кроме того, если горение
распространилось вниз до точки, отстоящей от нижнего края верхней опоры более
чем на 540 мм, провод или кабель считают не выдержавшим испытание.
Если образец не выдержал
испытание, проводят еще два испытания. Если в результате двух повторных
испытаний получены удовлетворительные результаты, провод или кабель считают
выдержавшим испытание.
ПРИЛОЖЕНИЕ А
(обязательное)
ИСПЫТАТЕЛЬНОЕ
ОБОРУДОВАНИЕ
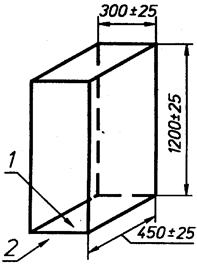
1 — неметаллическое дно;
2 — открытая передняя сторона
Рисунок 1 —
Металлическая камера
|
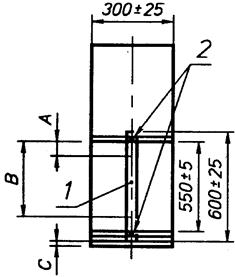
1 — образец; 2 — опорный
стержень и крепление медной проволокой; А — минимальная длина
необугленной части поверхности (50 мм),
В — максимальное расстояние до нижней
границы обугленной части поверхности (540 мм),
С — расстояние от дна
камеры до нижнего конца образца (около 50 мм)
Рисунок 2 —
Расположение образца в испытательной камере
|
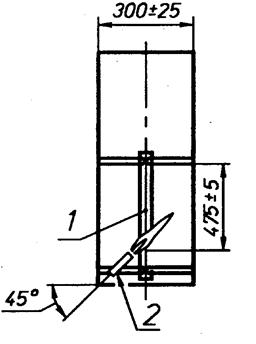
1 - образец; 2 - горелка
Рисунок 3 - Расположение
горелки мощности 1 кВт относительно образца
ГОСТ Р МЭК 332-2-96
ГОСУДАРСТВЕННЫЙ СТАНДАРТ
РОССИЙСКОЙ ФЕДЕРАЦИИ
Испытания кабелей на
нераспространение горения
ИСПЫТАНИЕ ОДИНОЧНОГО
ВЕРТИКАЛЬНО РАСПОЛОЖЕННОГО ИЗОЛИРОВАННОГО ПРОВОДА ИЛИ КАБЕЛЯ НЕБОЛЬШОГО
ДИАМЕТРА С МЕДНЫМИ ЖИЛАМИ
Tests on
cables under fire conditions. Test on a single small vertical insulated copper
wire or cable
Дата введения
1998—01—01
Предисловие
1 РАЗРАБОТАН И ВНЕСЕН
Техническим комитетом ТК 46 «Кабельные изделия» при АО «Всероссийский
научно-исследовательский, проектно-конструкторский и технологический институт
кабельной промышленности» (АО ВНИИКП) Росскоммаша
2 ПРИНЯТ И ВВЕДЕН В
ДЕЙСТВИЕ Постановлением Госстандарта России от 23 декабря 1996 г. № 681
3 Настоящий стандарт
представляет собой аутентичный текст МЭК 332—2—89 «Испытания кабелей на
нераспространение горения. Испытание одиночного вертикально расположенного
изолированного провода или кабеля небольшого диаметра с медными жилами»
4 ВВЕДЕН ВПЕРВЫЕ
1 ОБЛАСТЬ ПРИМЕНЕНИЯ
Настоящий стандарт
устанавливает метод испытания на нераспространение горения изолированного
провода или кабеля небольшого диаметра для тех случаев, когда метод,
приведенный в ГОСТ Р МЭК 332—1, не может быть применен из-за того, что при
приложении пламени могут плавиться токопроводящие жилы небольшого сечения.
Настоящий метод рекомендуется для проводов или кабелей с однопроволочными
медными токопроводящими жилами диаметром от 0,4 до 0,8 мм или с
многопроволочными токопроводящими жилами сечением от 0,1 до 0,5 мм2.
Стандарт устанавливает
также требования по оценке результатов.
Примечание— Соответствие
провода или кабеля настоящему стандарту не гарантирует предотвращение
распространения огня в любых условиях его прокладки. Поэтому, если риск
распространения огня велик, например при высоких вертикальных пучках проводов
или кабелей, нельзя делать вывод о том, что, если одиночный образец
соответствует требованиям настоящего стандарта, то и пучок не будет
распространять горение.
1.1 Нормативные ссылки
В настоящем стандарте
использована ссылка на ГОСТ Р МЭК 332—1—96 Испытания кабелей на нераспространение
горения. Испытание одиночного вертикально расположенного изолированного провода
или кабеля.
2 ОБЩИЕ ТРЕБОВАНИЯ
Настоящий метод
предназначен для типовых или других испытаний, и ссылка на него приводится в
нормативных документах на конкретные провода или кабели.
Образец провода или
кабеля после испытания в соответствии с разделами 6—8 должен соответствовать
следующему требованию:
после прекращения горения
расстояние от обугленной части тщательно протертого образца до нижнего края
верхнего зажима должно быть более 50 мм.
3 ИСПЫТАТЕЛЬНОЕ
ОБОРУДОВАНИЕ
Пропановая горелка в
соответствии с рисунком 1.
Если горелка не
соответствует рисунку 1, можно применить насадку, чтобы диаметр сопла горелки
составлял 8 мм.
Баллон с пропаном с
редуктором и манометром.
Металлическая камера следующих
размеров: высота — (1200±25) мм; ширина — (300±25) мм; глубина — (450±25) мм.
Передняя часть камеры
открыта, верх и низ должны быть закрытыми (см. рисунок 3).
Секундомер
Термостат
4 ОБРАЗЕЦ
Образцы длиной (б00±25)
мм отбирают от конца испытуемого провода или кабеля. Подготавливают два
образца.
5 КОНДИЦИОНИРОВАНИЕ
ПЕРЕД ИСПЫТАНИЕМ
Если провод или кабель
покрыт краской или лаком, образцы выдерживают в термостате при температуре
(60±2)°С в течение 4 ч, а перед испытанием охлаждают до температуры окружающей
среды.
6 УСЛОВИЯ ИСПЫТАНИЯ
Образец выпрямляют и
закрепляют в вертикальном положении в центре металлической камеры. К нижней
части образца прикладывают усилие 5 Н на 1 мм2 сечения
токопроводящей жилы так, чтобы
длина провода или кабеля
между нижним и верхним зажимами была (550±25) мм. Чтобы исключить малейший
поток воздуха, испытание следует проводить в соответствующем помещении, где
исключен сквозняк.
7 ИСТОЧНИК
ВОСПЛАМЕНЕНИЯ
Пропановая горелка должна
давать светящееся пламя при вертикальном положении и перекрытом доступе
воздуха. Расход газа регулируют так, чтобы длина светящегося пламени была
(125±25) мм (см. рисунок 2). Для этого на выходе редуктора рекомендуется
установить давление 1 бар. Затем горелку располагают в соответствии с рисунком
3. Ось горелки должна составлять угол 45° с осью образца. Расстояние между
торцом сопла горелки и поверхностью образца, измеренное вдоль оси горелки,
должно быть (10±1) мм. Расстояние от точки пересечения осей горелки и образца
до точки приложения усилия 5 Н на 1 мм2 сечения токопроводящей жилы
должно быть (100±10) мм. Расстояние от точки пересечения осей горелки и образца
до нижней части верхнего зажима должно быть не более 465 мм.
8 ПРОВЕДЕНИЕ ИСПЫТАНИЯ
Пламя прикладывают так,
чтобы оно обволакивало образец. К первому образцу его прикладывают в течение
(20±1) с. Если образец не разрушился, т.е. если токопроводящая жила не
расплавилась, результат испытания определяют в соответствии с требованиями
раздела 2. Если провод или кабель расплавился за время Т меньше, чем
(20±1) с, испытание повторяют на втором образце с длительностью приложения
пламени (7—2) с. В этом случае результат испытания оценивают только по второму
образцу.
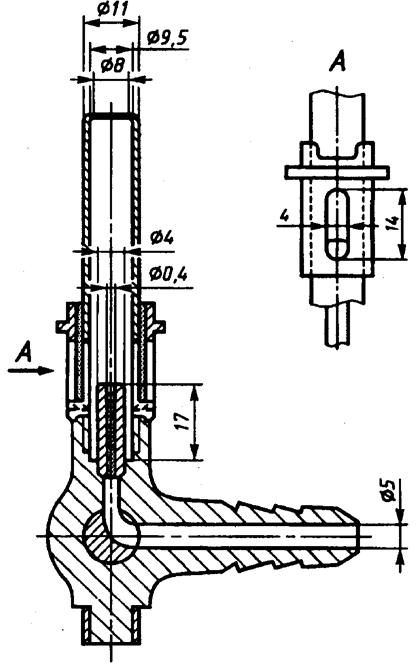
Рисунок 1 — Горелка
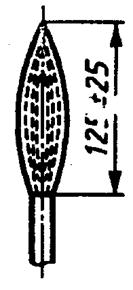
Рисунок 2 — Пламя горелки
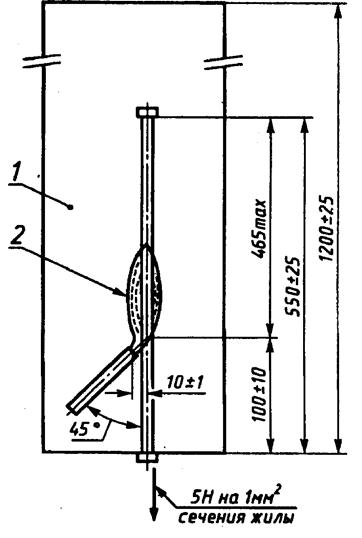
1—трехсторонняя камера; 2—
пламя, обволакивающее образец
Рисунок 3 — Расположение
горелки
ГОСТ Р МЭК 332-3-96
ГОСУДАРСТВЕННЫЙ СТАНДАРТ
РОССИЙСКОЙ ФЕДЕРАЦИИ
Испытания кабелей на
нераспространение горения
ИСПЫТАНИЕ ПРОВОДОВ ИЛИ
КАБЕЛЕЙ, ПРОЛОЖЕННЫХ В ПУЧКАХ
Tests on
cables under fire conditions. Test on bunched wires or cables
Дата введения 1998—01—01
Предисловие
1 РАЗРАБОТАН И ВНЕСЕН
Техническим комитетом ТК 46 «Кабельные изделия» при АО «Всероссийский
научно-исследовательский, проектно-конструкторский и технологический институт
кабельной промышленности» (АО ВНИИКП) Росскоммаша
2 ПРИНЯТ И ВВЕДЕН В
ДЕЙСТВИЕ Постановлением Госстандарта России от 23 декабря 1996 г. № 682
3 Настоящий стандарт
представляет собой аутентический текст МЭК 332—3—1992 «Испытания кабелей на
нераспространение горения. Испытание проводов или кабелей, проложенных в
пучках»
4 ВВЕДЕН ВПЕРВЫЕ
Содержание
Предисловие
1. Общие положения
1.1 Область применения
1.2 Нормативные ссылки
2. Общие требования к
проведению испытаний
2.1 Требования к образцу
и категории испытаний
2.2 Требования к
испытательной установке
2.3 Определение числа
отрезков
2.4 Крепление образца
2.5 Источник
воспламенения
2.6 Расположение
источника воспламенения
2.7 Проведение испытания
2.8 Оценка результатов и
проведение повторного испытания
2.9 Определение
кислородного индекса (КИ)
2.10 Выбор кабеля для
испытаний
3. Крепление образцов и
время воздействия пламени для испытания категории А, кодовые обозначения F/R и F
3.1 Выбор образцов
3.2 Крепление отрезков
3.3 Расположение образцов
3.4 Время воздействия
пламени
4. Крепление образцов и
время воздействия пламени для испытания категории В, кодовое обозначение F
4.1 Выбор образцов
4.2 Крепление отрезков
4.3 Расположение образцов
4.4 Время воздействия
пламени
5. Крепление образцов и
время воздействия пламени для испытания категории С, кодовое обозначение F
5.1 Выбор образцов
5.2 Крепление отрезков
5.3 Расположение образцов
5.4 Время воздействия
пламени Приложение А Метод определения кислородного индекса неметаллических
материалов кабелей
1 ОБЩИЕ ПОЛОЖЕНИЯ
1.1 Область применения
Настоящий стандарт
устанавливает метод испытаний по определению стойкости кабелей или проводов,
проложенных в пучках, к распространению горения независимо от их назначения,
например, силовые кабели или кабели связи (в т. ч. кабели для передачи
информации и оптические кабели) и т д.
Установлены три категории
испытаний, которые отличаются продолжительностью испытания и объемом
неметаллического материала в образце (таблица 1), они однозначно не связаны с
конкретными уровнями обеспечения безопасности при реальных способах прокладки
кабелей. Категория А имеет два кодовых обозначения для способов крепления.
1.2 Нормативные ссылки
В настоящем стандарте
использованы ссылки на следующие стандарты:
ГОСТ Р МЭК 332—1—96
Испытания кабелей на нераспространение горения. Испытание одиночного
вертикально расположенного изолированного провода или кабеля
ГОСТ Р МЭК 332—2—96
Испытания кабелей на нераспространение горения. Испытание одиночного вертикально
расположенного изолированного провода или кабеля небольшого диаметра с медными
жилами
ГОСТ 12175—90 Общие
методы испытаний материалов для изоляции и оболочек электрических кабелей.
Методы определения плотности. Испытания на водопоглощение и усадку
2 ОБЩИЕ ТРЕБОВАНИЯ К
ПРОВЕДЕНИЮ ИСПЫТАНИЙ
2.1 Требования к
образцу и категории испытаний
Образец должен состоять
из нескольких отрезков кабеля или провода (в дальнейшем — кабеля) длиной не
менее 3,5 м каждый, отобранных от одной строительной длины.
Общее число отрезков
кабеля в образце должно быть таким, чтобы общий номинальный объем
неметаллического материала в 1 м образца составлял для категорий:
А - 7 л;
В - 3,5 л;
С- 1,5л.
2.2 Требования к
испытательной установке
2.2.1 Камера и подача
воздуха
Испытательная установка
(рисунок 1) представляет собой вертикальную испытательную камеру шириной
(1000±100) мм, глубиной (2000±100) мм и высотой (4000±100) мм; пол камеры
должен быть приподнят над уровнем земли. Стыки стенок камеры должны быть
воздухонепроницаемыми. Воздух должен свободно поступать через отверстие
размерами (800±20) х (400± 10) мм, находящееся в полу камеры на расстоянии
(150± 10) мм от ее передней стенки.
Объемный расход
воздушного потока должен быть предварительно отрегулирован до значения (5000±500)
л/мин при температуре (20±10) °С и измеряться на входе или выходе камеры. Эти
характеристики должны постоянно контролироваться во время испытания.
Выходное отверстие
размерами (300±30) х(1000±100) мм должно быть в задней части верха
испытательной камеры. Задняя и боковая стенки камеры должны иметь
термоизоляцию, обеспечивающую коэффициент теплопередачи около 0,7 Вт/(м2
· К). Например, для стального листа
толщиной 1,5—2,0 мм достаточно покрытие слоем асбестовой ваты толщиной 65 мм
(рисунок 1а). Расстояние между лестницей и задней стенкой камеры — (150±10) мм,
а от нижней перекладины лестницы до пола — (400±5) мм. Расстояние от самой
нижней точки образца до пола камеры должно быть около 100 мм (рисунок 3).
2.2.2 Типы лестниц
Используют два типа
лестниц: стандартную шириной 500 мм и широкую шириной 800 мм. Конкретное
описание типов лестниц и способы крепления приведены в разделах 3—5 (см.
рисунки 2, 2а, 3, За-г).
2.2.3 Дымоочистительное
устройство
При необходимости
используют устройство для сбора и очистки дыма, выходящего из испытательной
камеры. Устройство, обеспечивающее сбор дыма, выходящего из камеры, не должно
влиять на скорость потока воздуха, проходящего через испытательную камеру.
2.3 Определение числа
отрезков
Для расчета требуемого
числа отрезков кабеля определяют объем неметаллического материала в 1 м одного
отрезка.
Образец кабеля длиной не
менее 0,3 м вырезают так, чтобы поверхности среза были перпендикулярны к оси
кабеля, что обеспечивает точное измерение его длины.
Образец разбирают и
каждый неметаллический материал взвешивают ( Сi ). Неметаллические
материалы, масса которых составляет менее 5 % от общей массы неметаллических
материалов, допускается не учитывать.
Если электропроводящие
экраны нельзя снять с изоляционного материала, эти компоненты принимают за одно
целое при измерении их массы и определении плотности.
Плотность каждого
неметаллического материала (включая пористые материалы) определяют
соответствующим методом, например по разделу 8 ГОСТ 12175, для получения
значений с точностью до второго десятичного знака. Для ленточных и волокнистых
материалов значение плотности принимают равным 1.
Объем Vi (л/м
длины кабеля) каждого неметаллического материала Сi определяют по
формуле
(1)
где Мi — масса
материала Сi, кг;
Рi — плотность материала Сi, кг/дм3;
l — длина образца кабеля, м.
Общий объем V
неметаллических материалов, содержащихся в 1 м кабеля, равен сумме отдельных
объемов V1, V2 и т.
д.
Ближайшее целое число
(0,5 и выше округляют до 1) отрезков, формирующих образец, получают делением
объема на метр кабеля, указанного в 2.1 для конкретной категории испытаний, на
общий объем V.
2.4 Крепление образца
Способы крепления
предварительно определенного числа отрезков, формирующих образец, приведены в
разделах 3-5
Для категории испытаний А
применяют два способа крепления (с кодовым обозначением F/R и F),
для категорий испытаний В и С — только один способ (с кодовым обозначением F).
Для идентификации можно
использовать следующие обозначения.
— категория А: кодовое
обозначение F/R — 332—ЗА F/R;
кодовое обозначение F
— 332—ЗА F,
— категория В, кодовое
обозначение F — 332—3В F;
— категория С, кодовое
обозначение F — 332—ЗС F;
2 5 Источник
воспламенения
Источником воспламенения
являются одна или две пропановые газовые горелки ленточного типа с
индивидуальными расходомерами и смесителями Вентури. Рабочая часть горелки в
виде плоской металлической пластины длиной (341±5) мм и шириной (30±5) мм имеет
242 отверстия диаметром (1,32±0,03) мм, расположенных на расстоянии 3,2 мм друг
от друга ступенчато тремя рядами по 81, 80 и 81 отверстий в каждом, при этом
образуется прямоугольник с номинальными размерами (257±5) х (4,5+0,5) мм, как
показано на рисунке 4. Поскольку отверстия в пластине могут высверливаться без
применения специального инструмента, допускаются небольшие отклонения от
указанного межцентрового расстояния. Кроме того, на каждой стороне пластины
могут быть высверлены небольшие вспомогательные отверстия, обеспечивающие
поддержание зажженного пламени.
Каждая горелка должна быть
снабжена устройством, контролирующим скорости подачи пропана и воздуха. На
рисунке 5 показан пример системы контроля Калибровка пропанового ротаметра
должна проводиться после монтажа при помощи расходомера для того, чтобы
трубопровод и смеситель Вентури не нарушали калибровку.
При изменении температуры
и давления по сравнению с установленными для пропанового ротаметра при
необходимости должны вноситься поправки.
При данном испытании
точка росы должна быть не выше 0 °С, объемный расход на входе должен быть
(76,7±4,7) л/мин, скорость
потока пропана должна
быть (13,3±0,5) л/мин при давлении 1 атм. и температуре 20 °С для обеспечения
интенсивности тепловыделения (73,7±1,68) · 106
Дж/ч или (20,5±0,5) кВт для каждой горелки.
Примечание — По величине
интенсивности тепловыделения определена скорость потока пропана.
2.6 Расположение
источника воспламенения
При испытании горелка
должна быть установлена на расстоянии (75±5) мм от передней поверхности образца
и на высоте (600±5) мм над полом испытательной камеры. Точка приложения пламени
должна находиться между двумя перекладинами лестницы на расстоянии (500±5) мм
от нижнего конца образца (рисунок 3).
Допускается проводить
регулировку потока воздуха и газа до испытания без установленной горелки.
Если используют две горелки
одновременно для испытания по категории А (с кодовым обозначением F) с применением широкой лестницы
(раздел 3), они должны быть расположены так, как показано на рисунке 4а.
2.7 Проведение
испытания
2.7.1 Условия испытания
Испытание проводят при
скорости ветра, измеренной анемометром, установленным на испытательной камере,
не более 8 м/с и при температуре внутри камеры не ниже 5 или не выше 40 °С.
Измерение проводят на расстоянии около 1,5 м над уровнем пола, 50 мм от боковой
стенки и 1 м от двери. Дверь камеры в течение всего испытания должна быть
закрыта.
Страницы: 1, 2, 3, 4, 5, 6, 7, 8, 9, 10, 11, 12, 13, 14, 15, 16, 17, 18, 19, 20, 21, 22, 23, 24, 25, 26, 27, 28, 29, 30, 31, 32, 33, 34, 35, 36, 37, 38, 39, 40, 41, 42, 43, 44
|